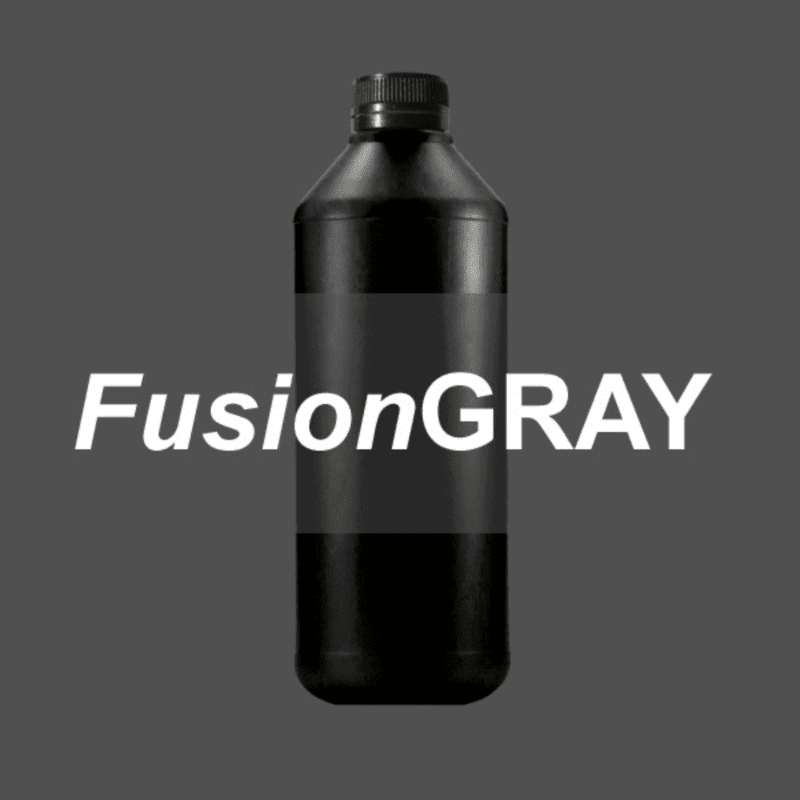
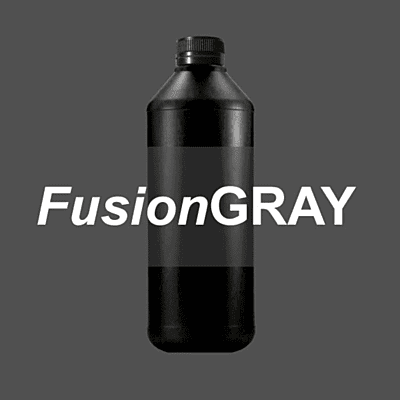
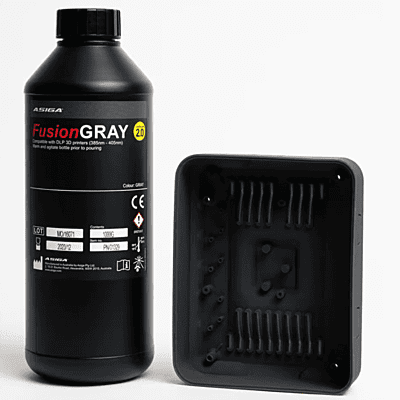
ASIGA FusionGRAY
$159.00 $265.00
High-temperature resistant material.
Stable at 160 °C / 320 °F, FusionGRAY is ideally suited to high temp applications where high compressive strength is required. Accuracy and sharpness of detail make FusionGRAY ideal for Injection mold tooling inserts or functional industrial casings to help you reduce time to market.
*IN STOCK SHIPS NEXT DAY*
Size
Choose Quantity
Product Details
Description, Indications & Effects:
Asiga FusionGRAY is intended be used in combination with DLP based 3D printers (i.e. Asiga Max Series or Asiga Pro Series) that support Asiga resins. Asiga FusionGRAY is optimised to build parts using light with 385nm or 405nm wavelength. Printer and resin must be optimized with respect to each other in order to produce complete and precise printed parts. If the printer and resin are not optimized with respect to each other this may have an adverse effect on the accuracy and physical quality of printed parts. DLP based 3D printers and post-curing lightboxes make use of a light source to polymerize the Asiga resin. Therefore, operators are advised to wear UV protective glasses when operating a 3D printer and/or lightbox. Differences in colour nuance may occur due to: production in batches; inadequate shaking and mixing of the original packaging before use; inadequate stirring in the FusionGRAY resin before use.
Preparation:
Ensure the 3D printer is clean prior to use, including the imaging area and any optical surfaces. Ensure the material tray is clear of solid debris prior to commencing a print. The presence of solid particles in the resin may cause deformation or failure of the printed objects. Nitrile gloves should be worn at all times when handling Asiga liquid resins up until the finishing step. Avoid contact with skin. If contact with skin occurs, wash thoroughly with cold soapy water. If contact with eyes occur, remove any contact lenses and flush with cold water and seek immediate medical assistance
Warming Resin:
FusionGRAY is solid at room temperature and must be liquefied prior to printing. This can be done any of the following ways:
- Warm the material bottle in a water bath: Place FusionGRAY bottle in a bath of warm water below 70°C until the FusionGRAY material melts. Ensure the lid on the bottle is secured tightly to prevent water ingress.
- Warm the material bottle in an oven: Loosen the lid of the bottle and place in a preheated oven at 70°C for 15-20 minutes or until FusionGRAY is liquid.
- Warm Build Tray in Printer: Place Build Tray inside a preheated printer and wait until the material is melted.
FusionGRAY is solid at room temperature and must be liquefied prior to printing. This can be done any of the following ways:
- Warm the material bottle in a water bath: Place FusionGRAY bottle in a bath of warm water below 70°C until the FusionGRAY material melts. Ensure the lid on the bottle is secured tightly to prevent water ingress.
- Warm the material bottle in an oven: Loosen the lid of the bottle and place in a preheated oven at 70°C for 15-20 minutes or until FusionGRAY is liquid.
- Warm Build Tray in Printer: Place Build Tray inside a preheated printer and wait until the material is melted.
Mixing Before Use:
In Bottle: Agitate/shake bottle vigorously prior to pouring for at least one minute. In Material Tray: Stir material with a soft spatula. Take care not to damage the film of the Material Tray. This step is necessary to re-disperse the (possible) pigment sediment from the bottom of the vessel. Colour deviation and print failures may occur if insufficiently mixed.
In Bottle: Agitate/shake bottle vigorously prior to pouring for at least one minute. In Material Tray: Stir material with a soft spatula. Take care not to damage the film of the Material Tray. This step is necessary to re-disperse the (possible) pigment sediment from the bottom of the vessel. Colour deviation and print failures may occur if insufficiently mixed.
Fill Material Tray:
Pour liquid resin into the material tray of the 3D printer. Place the material tray inside a preheated printer (see below) and close the chamber hood. Avoid exposing the material to direct sunlight.
Pour liquid resin into the material tray of the 3D printer. Place the material tray inside a preheated printer (see below) and close the chamber hood. Avoid exposing the material to direct sunlight.
Printer Settings:
When using FusionGRAY, the printer’s heater should be turned on to keep the material liquid when the printer is idle: On the Asiga printer’s menu go to Settings > Temperature > Controller ON. Change the Set Point to 40°C. See manual or user guides of Asiga 3D Printers (Asiga Max Series or Asiga Pro Series).
When using FusionGRAY, the printer’s heater should be turned on to keep the material liquid when the printer is idle: On the Asiga printer’s menu go to Settings > Temperature > Controller ON. Change the Set Point to 40°C. See manual or user guides of Asiga 3D Printers (Asiga Max Series or Asiga Pro Series).
Washing:
Wash parts in IPA 98%+ pure (Isopropyl alcohol) in a well ventilated area. Best results are achieved when using a pre and post wash. 1. Using an ultrasonic cleaning device: - Pre-wash bath: 2 minutes. - Post-wash bath: 2 minutes. Allow parts to dry thoroughly before post-curing.
Wash parts in IPA 98%+ pure (Isopropyl alcohol) in a well ventilated area. Best results are achieved when using a pre and post wash. 1. Using an ultrasonic cleaning device: - Pre-wash bath: 2 minutes. - Post-wash bath: 2 minutes. Allow parts to dry thoroughly before post-curing.
Post-Curing:
1. After washing and drying, let the printed parts rest for at least 30 minutes to ensure that the printed parts are free of alcohol residue.
2. Place the printed parts in UV curing unit “NK Optik Otoflash G171” for 2000 flashes.
3. Turn parts over and allow to cool.
4. Cure for a further 2000 flashes. Total: 4000 flashes (2 x 2000 flashes each side).
Post-curing is an UV-light treatment to ensure that FusionGRAY printed parts obtain optimal polymer conversion. Through this the residual monomer is reduced to a minimum and the required mechanical properties are obtained. We advise use of the NK Optik Otoflash G171 postcuring box. Place parts inside the G171 Otoflash chamber on the support mesh, do not use a plastic tray inside the chamber. Inert gas is not required. Please see NK Optik Otoflash G171 user guide.
1. After washing and drying, let the printed parts rest for at least 30 minutes to ensure that the printed parts are free of alcohol residue.
2. Place the printed parts in UV curing unit “NK Optik Otoflash G171” for 2000 flashes.
3. Turn parts over and allow to cool.
4. Cure for a further 2000 flashes. Total: 4000 flashes (2 x 2000 flashes each side).
Post-curing is an UV-light treatment to ensure that FusionGRAY printed parts obtain optimal polymer conversion. Through this the residual monomer is reduced to a minimum and the required mechanical properties are obtained. We advise use of the NK Optik Otoflash G171 postcuring box. Place parts inside the G171 Otoflash chamber on the support mesh, do not use a plastic tray inside the chamber. Inert gas is not required. Please see NK Optik Otoflash G171 user guide.
Investment Casting:
1. Use a standard gypsum bonded investment.
2. Use a standard phosphate bonded investment
1. Use a standard gypsum bonded investment.
2. Use a standard phosphate bonded investment
Storage Conditions, Expiry Date & Transport:
Store the resin in the original packaging at room temperature in a dry, cool and dark area. Close the packaging after each use. The expiry date of the product is mentioned on the product label along with the lot number. Store on printer for up to 4 weeks with hood closed or store in bottle for up to 24 months in a cool dark place. The product performance is no longer guaranteed once the expiry date is exceeded. Do not expose to UV-light. Standard transport conditions apply to this product. There are no restrictions for transport related to hazardous substances.
Store the resin in the original packaging at room temperature in a dry, cool and dark area. Close the packaging after each use. The expiry date of the product is mentioned on the product label along with the lot number. Store on printer for up to 4 weeks with hood closed or store in bottle for up to 24 months in a cool dark place. The product performance is no longer guaranteed once the expiry date is exceeded. Do not expose to UV-light. Standard transport conditions apply to this product. There are no restrictions for transport related to hazardous substances.
Waste Disposal:
Asiga resin in its polymerized form is not environmentally harmful thus can be disposed of in general waste. Asiga resin in its liquid state
should be treated as chemical waste. Special disposal requirements are applicable, check with your local, federal, or other regulatory agencies
for disposal requirements.
Asiga resin in its polymerized form is not environmentally harmful thus can be disposed of in general waste. Asiga resin in its liquid state
should be treated as chemical waste. Special disposal requirements are applicable, check with your local, federal, or other regulatory agencies
for disposal requirements.
Delivery Units:
Asiga FusionGRAY is available in 1 color only: Gray, 1kg.
Asiga FusionGRAY is available in 1 color only: Gray, 1kg.